ferro silicon manufacturing process
2020-04-16
The current domestic production of high quality silicon method, there are mainly five kinds, one is produced by selection of furnace charge high purity ferrosilicon, 2 it is to adopt the method of blowing chloride refining outside the furnace production of high purity and low carbon ferrosilicon, 3 it is to adopt the method of top blowing oxygen outside the furnace production of high purity and low silicon, aluminum four is adopt the method of thermal shock slag washing production of high purity and low carbon ferrosilicon, five is to adopt the method of selection of furnace charge low aluminum, low carbon ferrosilicon production
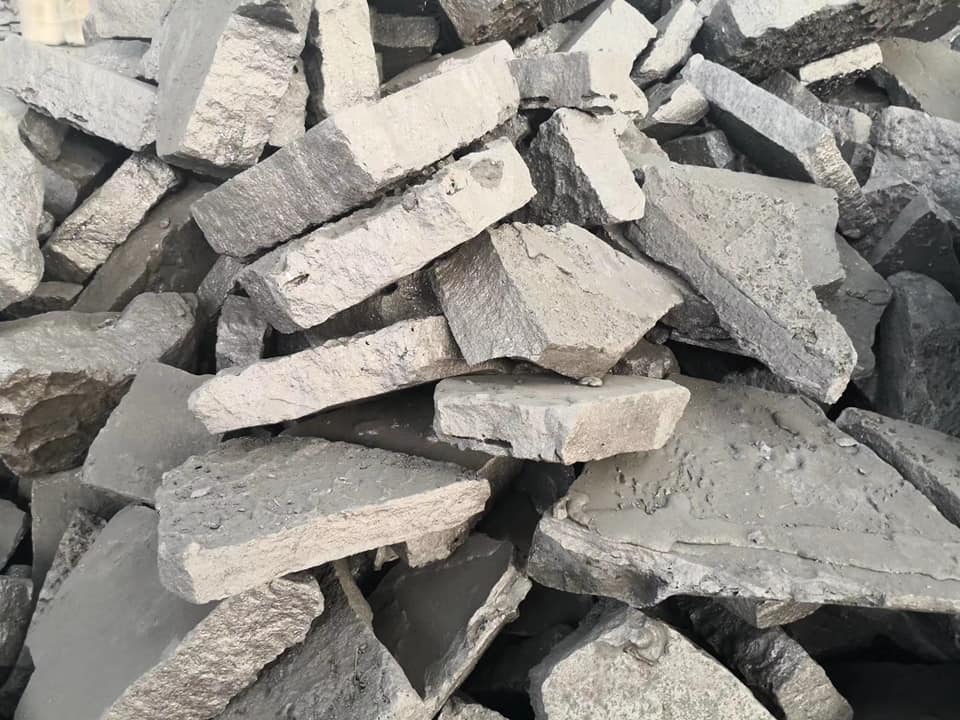
Ferrosilicon is a silicon-iron alloy composed of silicon and iron in a certain proportion and is mainly used for steelmaking, casting and other ferroalloy production. Ferrosilicon will react deoxygenation with steel, formula as: 2FeO+Si=2Fe+SiO2. So as to deoxidize oxygen and improve the quality of steel, including enhance the hardness, intensity and toughness, also increase the magnetic conductivity. Melting point of ferrosilicon is 1290-1360 degree centigrade. The density of ferrosilicon depends on silicon percentage. When the silicon content is higher, the density of ferrosilicon will be higher accordingly. The regular density of ferrosilicon 75 grade is 3270kg/m³.
Conventional ferrosilicon models including FeSi75, FeSi72, FeSi65. The ferro silicon manufacturing process of those models are same. Raw materials: coke, iron ore, silica stone. Requirement to raw materials in ferro silicon manufacturing process: Silica stone SiO2 purity above 97.5%. No sand, dust or other impurities on the surface. Size ranges between 80-140mm. Coke with fixed carbon no less than 82%, size 8-18mm, moisture below 16%, volatile matter below 8%, ash content below 8%. The main chemical equation of ferro silicon manufacturing process is SiO2+C=Si+CO. The whole reaction procedure includes four part: 1, disproportionated reaction of SiO. 2, Form of Silicon Carbide. 3, chemical decomposition of silicon carbide, formula SiO2(L)+ 2SiC(S)=3Si(L)+2CO(g). 4, Liquid CO2 react with SiC and to form Silicon, SiO2 gas and CO gas, formula 3SiO2(L)+ 2SiC(S)=Si(L)+2CO(g)+ 4SiO(g). The main facility for ferro silicon manufacturing process is electric-arc furnace. The Si content should be adjusted by raw material adding amount. After general ferro silicon manufacturing process, refining procedure is also necessary in order to remove Aluminum, Calcium, Carbon and other harmful elements.
Sizing is also a very important part of ferro silicon manufacturing process. Standard lumps are easy to use as deoxidizing agent for steel factory. It’s crashed and then selected to 10-50mm, 50-100mm. Grains are easy to be used as ferrosilicon inoculant. Gain size usually are 1-3mm, 3-8mm, etc. Ferrosilicon powder can be used as flotation agent for various kinds of minerals. And atomized fesi powder are used as electrowelding materials. After those method, the ferro silicon manufacturing process will be complete and ready to be packed and delivered to users.